2 Important Factors to Consider When Using Metal Material for Your Project
Have you created a unique design for a particular application and will need sheet metal material to bring your idea to life? Have you been asked to construct and install custom metal components but are unsure about the types of heavy-duty machinery you will need for the project? Are you wondering whether or not you should tackle these types of situations on your own? If yes, then here are 2 important factors to consider first before you begin your project.
Cost
When it comes to fabricating sheet metal of any kind, you will need special equipment to complete the project. Welding machines, cutting machines, and sanding machines are to only name a few types of equipment you may need. As you know, these pieces of equipment will cost you a significant amount of money to procure. You will also need to consider the cost of acquiring the particular type of sheet metal you will be using.
Precision Work
Just like procuring all the pertinent equipment for your project, precision is another important factor to consider before you begin your project. While the equipment mentioned above can help you fabricate sheet metal material or metal components, you will also need the necessary skills for precision work.
What You Should Do Instead
Perhaps you are beginning to feel overwhelmed when considering these two factors for your project. Here is a tip. Consider utilizing the services of a company that offers custom sheet metal fabrication services. The professionals at Vista Manufacturing Company offer over 50 years of custom sheet metal fabrication expertise and can help you with your project needs. So, when searching for a highly knowledgeable and experienced company that specializes in metal fabrication, they are the only ones you should contact.
The post 2 Important Factors to Consider When Using Metal Material for Your Project appeared first on Vista Manufacturing Company.
You might also like
Vista Manufacturing Blog
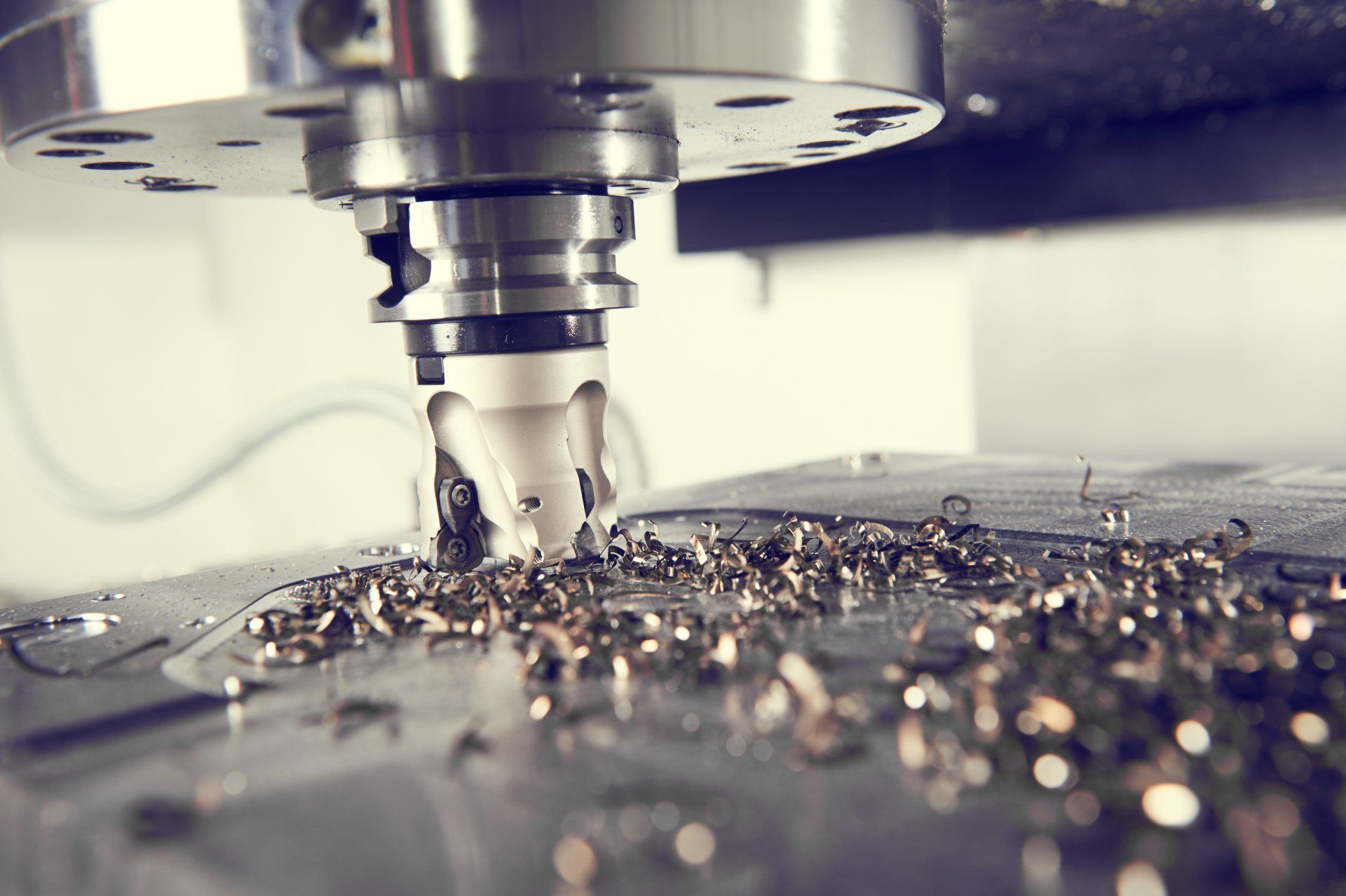
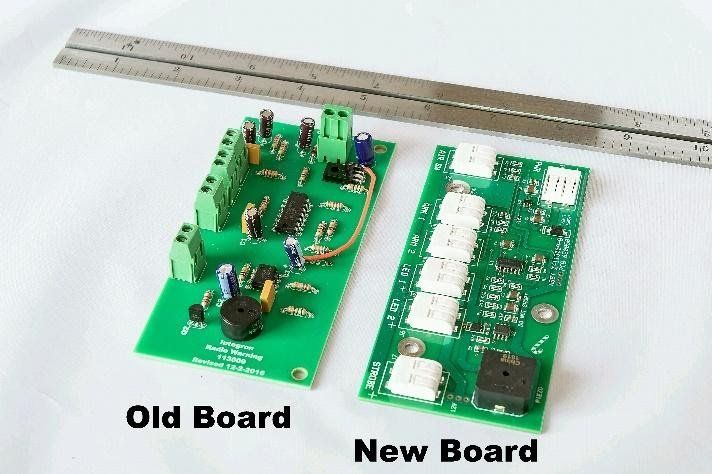